SONYの最上級ヘッドホン『MDR-Z1R』。開発者のお2人にお話を伺いました。
だいせんせいです。
皆さんは、MDR-Z1Rというヘッドホンをご存知ですか?
2016年発売、SONYのヘッドホンの歴史の中でも指折りのフラッグシップモデルとして登場したMDR-Z1R。
同じく超高額なハイエンドウォークマン『NW-WM1Z』と同時に発売されたこともあり、大きな注目を集めたことは今なお記憶に新しいことと思います。
そんなMDR-Z1Rは、歴代のSONYのフラッグシップヘッドホンのDNAを受け継ぎ、かつ、現代のハイレゾシーンを象徴するような高い完成度を持つ、素晴らしいヘッドホンです。
ただ、その開発が決して楽でなかったであろうことは、想像に難くないでしょう。
今回の記事では、そんなMDR-Z1Rの開発秘話を徹底紹介!
同機の開発者である潮見 俊輔氏、尾崎 雄三氏のお二人にインタビューさせて頂きました!
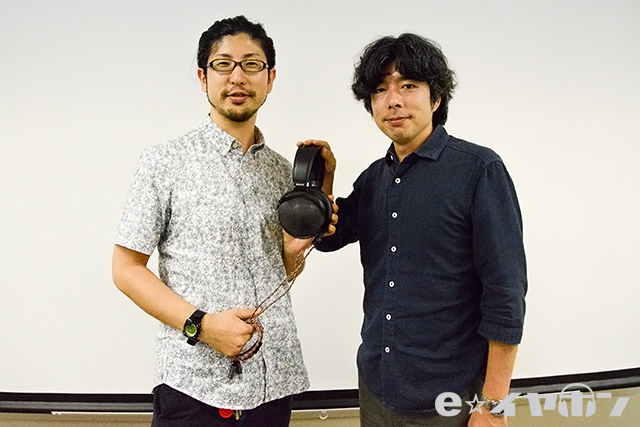
左から音響設計の潮見さん、プロジェクトリーダーの尾崎さん
MDR-Z1Rの『空気感』の三要素
先ほど投野が話していたように(※)、SONYのヘッドホンの歴史というのがあって。
MDR-CD900STからQUALIAと来て、ハイレゾの世代になり、空気感を向上させたという話をしました。
その『空気感』の部分に関して最初に説明しておくと、その後わかりやすくなりますので。最初にその説明をさせてください。
(※ 前回記事参照)
今回このモデルを開発するにあたって、『ヘッドホンにおける空気感』のために定義した物があります。
まず第一に『広帯域再生の実現』。
ハイレゾ対応ということで再生周波数帯域を伸ばし、今回は上限が120kHzまでとなっています。
ただ、実は下の方も力を入れています。
近年はレコーディング技術の進化もあり、より低い帯域を音源に入れることが出来るようになりました。
また、収録された部屋が広ければ広いほど、その大きさに見合った長い波長の低い音が空間表現として一役を担っている。
そういった再現性を高めるために、より広い帯域の再生を実現させました。
次にダイナミックレンジですね。
物凄く大きな音から小さな間接音や反射音まで、正確に再現出来るというところ。
これが、ハイレゾ音源が一般的になってくることによって、我々が得られる空気感を感じる事ができる要素のひとつです。
最後に平面波形。
今回は、一般的な耳のサイズよりも大きな70mmのドライバーユニットを使っています。
というのも、普段から我々の生活で耳に届いているものが平面波なんですね。
音の発生源があって、それが耳に届くまでに平面に近い状態になっていく。
そこを再現することで、よりリアリティのある音になると。
今回はその3つを抑えて、設計をしていきました。
MDR-Z7でも空気感の再現というテーマでやりましたけども、
そこからMDR-Z1Rにむけて、さらなる空気感というものを求めました。
その部分というのが、MDR-Z7からMDR-Z1Rでの技術的な差に表れています。
例えば、先程挙げた広帯域再生ですね。
後ほど説明しますが、これは振動板にマグネシウムを使うことによって実現しています。
また、二番目に挙げた広ダイナミックレンジについても、70mmという大きなドライバーユニットを使うことに加え、マグネットの大型化をしています。
まず、70mmというドライバーサイズについて説明します。大きい音を再生すると、振動板が動いた際の空気を押し出す量が多いんです。
ドライバーの口径が大きいと、押し出すときに変形量が小さく済むので、歪みが乗りにくいなどのメリットがあります。リニアリティが高いわけです。
また、ハウジングもそうですね。
この『レゾナンスフリーハウジング』を採用することで、再生される音源以外のノイズや、外部から入ってくる音を排除しています。
それにより、ハウジング内の空間の共鳴が起こらなくなり、暗騒音をより静かな状態に持っていくことが出来るため、音源の小さな音も再現することが出来ます。
まとめると、マグネシウムドーム振動板は広帯域再生に結びついており、
レゾナンスフリーハウジングは広ダイナミックレンジに結びついています。
MDR-Z1Rで実現した、マグネシウムドームの採用
では、マグネシウムの良さについて熱く語りたいと思います(笑)。
一般的に我々の身近な『軽い金属』というと、一円玉で使われているようなアルミニウムなどが多いですが、今回はマグネシウムを、振動板の真ん中のドームの部分に使っています。
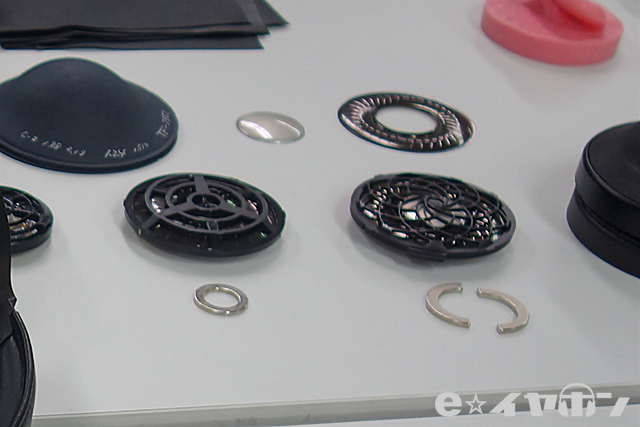
MDR-Z1Rのドライバーユニット(写真右)。
なぜマグネシウムを採用するのかというと、アルミと比べても(同じ体積で)重量がおよそ2/3ぐらいなんです。
そのため、アルミニウムよりも同一重量での剛性が高く、強度があるんですね。
さらに言うと、『内部損失』というのが高いんです。
例えば通常の材料である金属やガラスなどを叩くと、カンカン、と音が鳴る。あれは内部損失が低いために、材料固有の音が鳴っているんです。
逆に紙などは内部損失が高く、叩いても音が鳴らない。
そういう観点で見ていくと、金属の中でも比較的内部損失が高いのがマグネシウムなんです。
その『硬い』『軽い』『内部損失が高い』というところが重要でして。
高い周波数を再生する時、振動自体は小さくなっていきますが、反面ドライバーユニットが物凄く早く動くので、ドームのところで分割振動が発生します。
そういった物を抑えて、ボイスコイルから発生している振動をロスなくドームの部分に伝えるために、マグネシウムを使っています。スピーカーなどでツイーターに使われたりするのも同様の理屈ですね。
金属において純度って結構大きな要素だと思うのですが、『どのマグネシウムが良かった』というのはありますか?
音響特性と製造面の両方を検討して採用しています。
選ぶ過程としてはどのプロセスで選んだのでしょうか?
例えば開発の中盤あたりで、マグネシウムに変えてみたら良くなった、とか。
本当を言うと、10年以上前の話になります。
なるほど、10年。……10年!?
素材として優れているので、アイデアとしては昔からありました。
ただ、ヘッドホンの振動板って、物凄く軽く作らないといけないんです。特に、高い帯域を出すためには。
スピーカーだと結構パワーを入れられるんですけど、ヘッドホンはスピーカーと比べるとパワーも弱く、軽い振動板じゃないと動かないので、なるべく薄く伸ばしたものを使う必要があるんです。
技術の進化によってここまでの薄さに出来るようになり、振動板として使えるようになったのが本当に最近のことです。
振動板の中で、ドーム部分というのは変形してほしくないので、とにかく軽くて硬い必要があるんです。
そのために理想的な材料というと、やはりマグネシウムになるわけです。
ですので、それこそ10年以上前から『マグネシウムはドームに最適な材料なんじゃないか』と考えていて、ようやく薄くプレス出来るようになったのが、2013年ごろ。
そこからさらに3年かけて、2016年まで色々と研究を重ねてきました。
マグネシウムを薄く延ばすこと自体がまず難しいですし、さらに言うと、ドームの形状のためにちょっと絞るというのが、これまた難しい作業でして。
マグネシウムという素材は、筐体などであればよく使われています。その場合は、例えば厚みを0.8mmから0.6mmにする、といったオーダーなんです。
対してこれは、30ミクロン(0.03mm)を切るという薄さなので、一桁変わってくるんですね。
そうなると、物作りとしても随分変わってきます。
薄く、かつ破れないようにプレスするというのは、世界でもなかなか出来るところが無いんです。
なので、国内にある小さな工場で生産しています。
普通の金属プレスというと、大きな機械で『ガシャン!』ってやるじゃないですか。
でも、今回のマグネシウムドームの場合はゆっくりとプレスするんです。
だから、大量生産が難しいんですね。頻繁にガシャンガシャンと出来るようなものでもないので。
何年もかけてマグネシウムの研究をしていて、『ようやくプレス出来るようになった!』と連絡が入ったんですね。
観に行ってみると、イメージしていたプレス機とは全然違う、小さな機械が置いてあって。『これはなんだろう?』と、なるわけです。
話を聞いていくと、本来はプレス用じゃない機械を、工場のおじさんが魔改造してプレスしていて。世界に一台の機械だったんです。
技術力の塊みたいなエピソードですね。
ただ、実際に量産化していった時、たった一台の機械が壊れてしまうととんでもないことになるので(笑)。
今はもう一台作って頂いて、それで量産が出来ています。
出来上がったマグネシウムドームを更にドライバーユニットのエッジの部分に貼り合わせるんですけど、これもシビアな精度が求められます。
ゼロコンマ何mmというズレがあったり、ボイスコイルの取り付けが浮いていたりすると、本当に狙った特性が出ないんですよ。
なので実はこれも、SONYのバランスド・アーマチュア・ドライバーを製造しているような精密なコントロールが出来る工場でやっています。
そういうところがあって、ようやく120kHzまでの音が出ている。曲面と曲面を隙間なく貼るって、難しいんですよね。
MDR-Z1Rのために開発された、2つに分割されたマグネット
あとは、ドライバーユニットに使われているマグネットについても話しましょう。
一番小さいものが、40mmのドライバーユニット用のマグネット。
真ん中のサイズが50mmのドライバーユニットや、Z7の磁気回路などにも使っているマグネット。
そして一番大きなものが、MDR-Z1Rで使っているマグネットです。
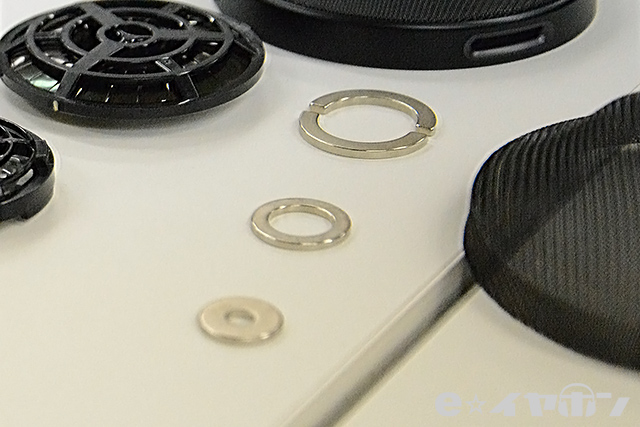
手前から順番に、40mmドライバー用、50mmドライバー用、MDR-Z1R用。
2つに分かれた形になっていますが、実はこれにはちゃんとした意味があります。
一口にマグネットと言っても色んなグレードがあって、ネオジムマグネットの中でも、量産可能な中で最高磁力の物を使っています。
そうなってくると、作り方も結構特殊になってくるんですね。
材料自体は一緒なんですけど、成形の方法が変わってきます。
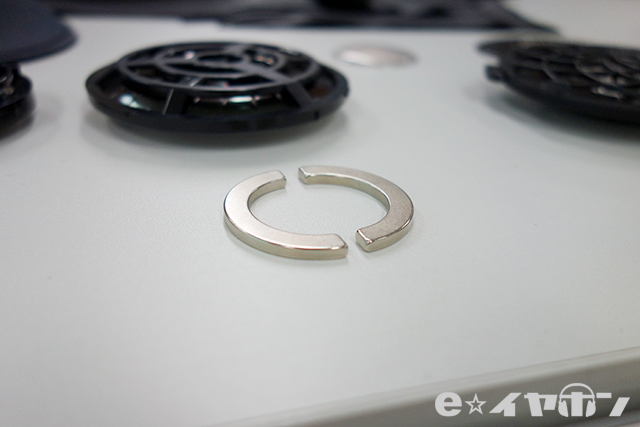
2つに分割して成形されたネオジムマグネット
マグネットの製法として一般的に普及しているのは『縦磁場成形』と呼ばれる方法で、小さな磁性粉という粒をプレスして押し固めながらプレスと同じ方向に磁界をかけて磁石にしていくという方法で、たくさん磁石を作れるんですが、磁性粉の方向が少し傾いてしまうんです。そのため材料の性能をまだ最大限に使い切れていないんです。
それに対して、今回はプレス方向と垂直に磁界をかけてやる『横磁場成形』を行うことで配向の傾きを抑え、マグネットの性能を最大限に引き出すことで、高い磁気特性を保っています。
ただしこの成形方法だと、70mm用という大きなサイズを作るのはなかなか難しい。そのために、2つに分割してつなぎ合わせて使っているわけです。
これも当然、日本の工場で作っています。凄く作りにくいので、あんまりやらないんですけどね、こういうことは(笑)。
なんでここまでやっているかというと、マグネットの磁力を高めることで、先ほども挙げたダイナミックレンジが広がるためです。
要は大口径マグネットという大きなエンジンを積んでいる状態です。駆動力が上がれば、十分に小さな音から大きな音までを余裕を持って再生出来るわけです。
やはり音を聴き比べると、立ち上がりとかが全然変わってくるんですよ。
やはりそうなると、これは絶対使いたいな、ということになりまして。
このような基本性能を高めつつ、筐体側の方も併せて調整をしていきました。
通気する『密閉型』。MDR-Z1Rの筐体デザイン
筐体も、凄く良いデザインですよね。月次な言い方ですけど、飽きが来ないというか。
ええ、そうですね。ここだけの話ですけど、初めてデザインを見た時、正直『ちょっと地味かな』って思ったんです(笑)。
デザイナー曰く、音を作るための要素や技術をそのまま形にして、それ以外の要素を削ぎ落としたと。
例えばこのハウジングの形状も、技術的な面で、ちょっと理由があって。
空間を作ってる、というようなことでしょうか?
そうですね。
必要な容積を確保しつつ、あとは細かい配慮として、中で斜めに配置されているドライバーユニットを避けるような形状でもあるんですけど、さらに、ホームオーディオのセッティングのように、対抗面が出来ないように工夫されています。
ユニットに対して対抗な面があると、反射や共鳴が発生するためです。
それに加えて、丸い曲面を合わせることで、形状的な剛性を持たせて機械的な共振も取り除くように気を使った形になっています。
先程のマグネシウムの話じゃないですけど、ハウジングに関してはどれくらい研究されていたのでしょうか?
レゾナンスフリーハウジングの、通気する素材に関していうと、これも10年以上は検討してますね。
QUALIAなど、過去に研究してきた技術の延長上にあります。
通気のコントロールを突き詰めていった結果ですね。
大きさの感じで言えば、『(MDR-Z1Rが)MDR-R10に似てる』って、よく言われるんですよ。
「どっちが音が良いんですか」とかも。それはもちろん、人の好みに依るところがありますけど。
そうですよね。人それぞれ、聴こえ方も違うし。
よい音を突き詰める、というところはMDR-Z1RもMDR-R10も同じですが、そこに至るまでのアプローチが異なります。
MDR-R10のアプローチは、木の筐体の響きを活かすというコンセプトから来てるんですね。
しかしMDR-Z1Rに関しては、音声信号から振動板が生み出す音に対して、余計な音を乗せない。
筐体の共鳴も乗せないし、ハウジングを通気させることで、入ってくる外音も乗せない。振動板自体もそうです。材料固有の音もなるべく乗せない。
そういったところに、気を使って作っていたんです。MDR-R10とは異なるアプローチで、良い音を追求しました。
通気するハウジング、音響レジスターがこれです。
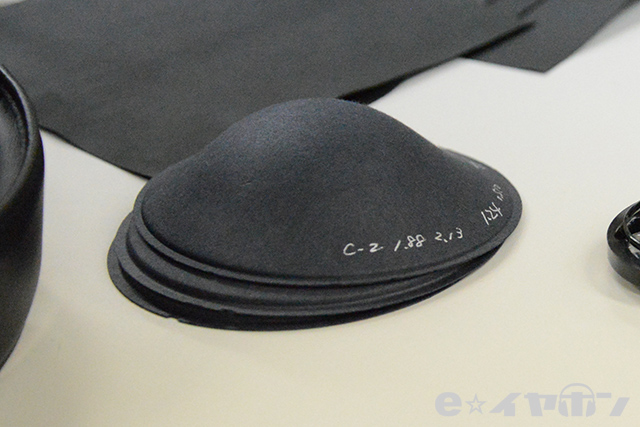
カナダ産の針葉樹と、日本の雪解けの地下水から作られるパルプ製音響レジスター。
ハウジング全体から非常に僅かな通気をさせたくて、かつ、シビアな範囲に通気量をコントロールしたい。
そのために化学的な用途のフィルターや、水・油を通すものとか、色々な材料を探しました。
そうして色んな遠回りをして、最終的にやっぱり立ち返ったのが、我々がQUALIAからずっと研究してきたこの素材になります。
ほぼ無いんじゃないかっていうくらいの、本当に僅かな通気です。
密閉型と言っている所以がまさにそこです。Z7と比較しても大差なく、ほとんど音漏れが無いんです。
この材料も、語ると色々長くなっちゃうんですけど(笑)。
これも、すごいですよね。
日本の雪解けの水がどうとか、カナダの針葉樹とか……。
文字面だけ見ると「オカルトじゃないの」なんてよく言われます(笑)。
ただ、もちろん全て、ちゃんとした意味があるんです。
僅かな通気っていうことは、スカスカじゃ駄目ですし、強度が無いペラペラのものでも駄目です。
なので繊維長が長く、かつ密度の詰まっている針葉樹を探したらカナダ産のものに行き着きました。
そこが大事な要素ですね。
あとは、地下水。日本の雪解けの地下水を使用しています。
これも、普通に飲んでも美味しいんですけど(笑)。
温度が常に均一なので、水として品質が安定しています。それによって量産自体の品質が保たれる。
日本の水が軟水というのも良いんです。
例えば紙を作った時に、その紙がどれくらい長持ちするのか。そこには不純物が無い方がいいんですよね。
日本の水でやってるのはそういう理由なんです。
繊維長や抄くときの水の性質が違う洋紙と和紙で見ても、やっぱり洋紙って、100年持てば良い方なんですけど。
和紙はもっと長く、1000年単位で残ったりするので。
この材料っていうのは、スピーカーの振動板などにも使われるものなんですね。
これも内部損失が高い材料ですから、これ自体の余計な響きが無い。
通気のコントロールに関しても、測定器とかを全部ゼロから作りました。
生産する工場で厳しく測定出来るようにして、管理しています。
通気材料を探していく上で、織物とか編物とか、そういった繊維系の物も出てくるんです。
例えば織物なら『西陣織』って何なんだろうとか。編物で言えば、セーターの編み方とか、そういうのに詳しくなったり(笑)。
そんな寄り道を色々として、最終的にはそれが、ハウジングのプロテクターに生かされたりもしています。
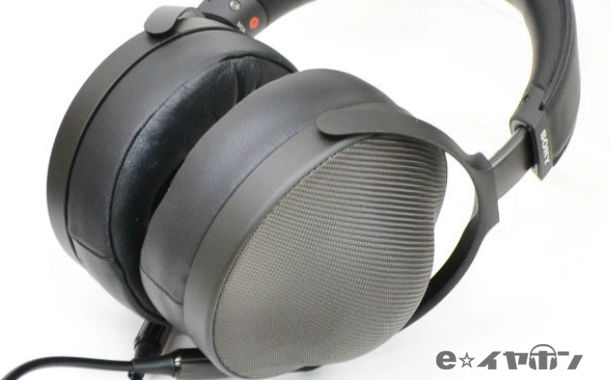
ハウジング全体がステンレスメッシュのプロテクターに覆われている
なるほど!
金網にも、いろいろな目というかパターンがあり、それについて研究していくと面白いことに、結局織物のパターンに帰ってくるんですよね。
繊維を織っていくのか、ステンレスの線材を織っていくのか。それらの技術が、実は同じところで繋がっていた。
ただ、織ったステンレスの線をプレスするというのも、なかなか難しい技術で。
日本の職人さんの意地と、こだわりで実現して頂きました。……ちょっと怒られながら(笑)。
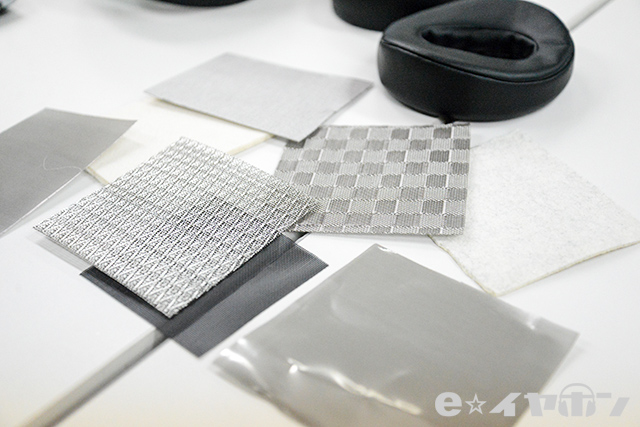
音響レジスターやハウジングプロテクターを研究する過程で生まれた、数々のサンプル。
これはどれくらいかかったんですか?
まるまる3年くらいはかかってるかもしれません。
3年! これまた長いですね!
このハウジングプロテクターも、どこでも作れるというものではなくて。
お風呂の排水口のフィルターみたいなものであれば簡単に作れるのですが、この複雑な形って、なかなか出来ないんですよね。
ちょっと中心がズレてますもんね。
これもメカ的に言うと、共振点がちょっとズレている形です。
スピーカーのインシュレーター等と同様の思想ですね。
『3Dデータと手作業の融合』MDR-Z1Rのイヤーパッド
あとは、イヤーパッドですね。
そうですね。
装着の快適性と音質、両方を担うパーツなので、かなり重要な部分です。
SONYでは従来から耳型を集めて、それに併せて内側のユニット配置を傾けて、という作り方をしてきました。これは、実はMDR-R10でも行っています。
そこで『2016年の技術で何ができるか』と考えたんですね。
今は人の頭を3Dスキャンで取れる時代なので、我々も当然その技術を持っていて、最初はそこをベースに作ってみたんです。
そうすると、非常に急な角度の形になったんですけど、データ通りに作ったんだからぴったり行くんじゃないか、と思ったんですね。
でも、実際に着けてみると、これがあんまり……。
平均のデータで取っちゃうと、人って、ばらつきがありますから。
あとは3Dデータって、クッションの潰れとかをあまり加味出来ないんですよ。
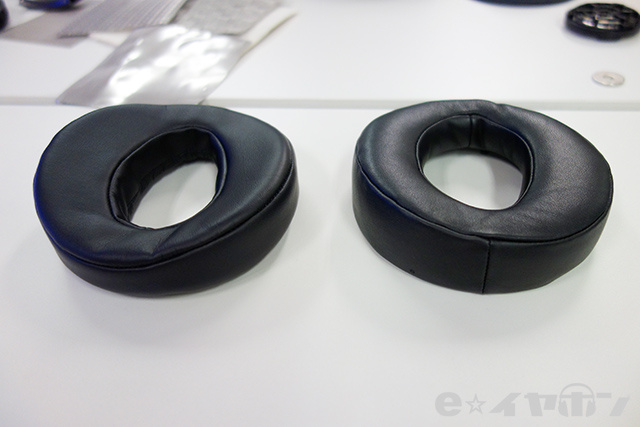
左がプロトタイプ、右が製品版のイヤーパッド。形状が大きく異なる
人の頭を3D化して、面を取って、平均化するとこの形(上図左)になるんですね。
でも、装着してみて違和感がある部分を手作業で修正していくと、最終的にはこういう形(上図右)になっていく。
2つを比べたら、全然違いますね。
やはり肌に触れる部分がポイントで。荷重によって潰れが異なるんですね。
今は技術が進歩していて、デジタルのデータがあるから、全部を数値化できるんじゃないか? って思ってしまうんですけど。
やはり最後は人が着けたり、音を聴いたりして『良い』『悪い』って感じるものなので。
データだけで出来るものではない、というところがあります。
見た目で言うと、プロトタイプの方がフィットしそうに見えるのに……。
見た目で言うと、そう見えちゃうんですよね(笑)。
一般的にも『こっちだ!』って感じがするんですけど。我々も最初は、そう思っていたくらいなので。
どこにどれだけ荷重がかかっていると気持ち悪いのかっていうのが、あるんですよね。
あとは形状として大事なのは、音響的に、空気の漏れがないこと。
正しく聴くためにはここの部分の密閉がすごく大事なので、潮見に言わせると『イヤーパッドは音響のメインです』と。
潰れるということは、空間の大きさが変わるということなんですよ。
そうすると、音が変わりますよね。
そして『MDR-Z1R』は完成へ
そうやって個々のパーツを非常にこだわって作られてきたということですが、実際に組み込んでみると想定と違った、というようなことはありましたか?
ありますね。
例えば、シビアに通気をコントロールしているレジスター。
レジスターの寸法はきっちりでているはずなのに、なぜか特性が違う、ということがありました。
これは、レジスターの素材自体が柔らかいものなので、正確に組み合わせても、時間が経つとわずかに浮いてきたりしてしまったんですね。
突き詰めていくと、やっぱりそういうところからの空気漏れが原因だったりするので。
密閉がしっかり取れる構造を、どうやって量産に落とし込んでいこうか、というところにかなり気を使いました。
最終的には、簡単に高域・中域・低域と3つに分けたとして、どこをどういう風に調整していったのでしょうか?
ボーカル……に限った話ではありませんが、中域の音色のバランスとか、そういうところが音楽の要素としてはかなり多いんです。ソニーのヘッドホンは全て、まずはここを整えてから全体を調整していきます。
また高域については、ハイハットの音色や消えざまが自然になるよう調整していきました。
あとは、低域ですね。音楽のグルーヴを生み出す低域に対する音の熱意って、欧米の人の方が強く持っているな、っていうのがあって。
MDR-CD900STも当時音の調整で筐体に穴を空けたという話をしましたが、MDR-Z1Rもソニー・ミュージックのニューヨークのスタジオで同じようなことをやってるんですよ。
ニューヨークのスタジオ!
そこでヘッドホンのチューニングを行っていたということですか?
そうですね。
実際にスピーカーと聴き比べて、最終的な筐体内の圧力や空気のコントロールを行っていくんですが、スタジオには測定器も何もないので。
そのスタジオのエンジニアが言っていることを自分の中で理解して、エンジニアリングで「ここの周波数をこう上げたいな」って思った時に、経験とかノウハウから、どこをどうすればどうなるっていうのは解るので。その感覚を頼りに穴を空けたりしていました。
まさに職人ですね……。
厳正な話をしつつ、ミュージシャン的な「もう少しグッとくる感じで」っていうようなリクエストもあるので、そこをどう落とし込めば作れるかな、というのを考えて。
実際にその場でパーツを外して、ドリルで穴を開けて、レジスター類も張り替えたりとか。
投野さんの技術を受け継いでいるんですね。
会社に入る前は、(MDR-CD900STの穴を見て)何の意味があるのかわからなかったんですけど、どんどん継承していく上で、その場で調整できるくらいまでスキルが磨かれていったんです。
ニューヨークで共に音づくりをしてくれたのが、マーク・ワイルダーさんというマスタリングエンジニアで。
本当に様々なジャンルの曲でマスタリングされてきた方なんですね。
グラミー賞を何個も持たれてる方なんですよ。
当然、ジャズとかクラシックもあるんですけど、ポップスとかもそうで。
「こういう音が世界で求められている」というのを知っている人なんです。
私自身もマークさんから、日本の音楽とはまた違った感覚を学びながら、MDR-Z1Rの音を形づくっていけたと思います。
下の方まで音がしっかり伸びているというのが、結構大事で。
イヤーパッドで密閉をしっかりとらないと、低域がどんどん漏れていっちゃうんですね。
ボワついたりとかも、色々ありますよね。
そうですね。
タイトに、なおかつ柔らかさもありつつ、みたいなコメントをもらいながら。
それなら、どこをどうすればそういう音になるかな、というのをやってきました。
その辺もあって、我々はMDR-Z1Rをこだわりを持って『密閉型』と呼んでいます。
低域もしっかりと出していきたい。
ここに辿り着くまでが、本当に大変でした。
ニューヨークと行ったり来たりしなければならないので、強行スケジュールで行くことが多くて。
全体で見れば10年がかりの長いスケジュールなのに、ここは強行なんですね(笑)。
ギリギリまで詰めてからニューヨークに行くから、時差ボケを残しながらスタジオに行ったりもしました(笑)。
そこで貰った宿題を持ち帰って、一ヶ月かけてまた次の試作をして、それをまた聴いてもらって……の、繰り返し。
ただ、もちろん素晴らしい経験も多々ありました。
スタジオの隣に、『バードランド』っていうジャズクラブがあったり、音楽が身近な環境でもありました。
「今日、こういう人がライブやるからオススメだよ」なんて紹介もしてもらって、実際にジャズクラブに行ってみたりもしました。
そこで生音を聴いて勉強して、空気を感じて。
やっぱり、自分でお金を払って聴くモチベーションって大事だなって思うところがあるんですよ。
特性を追い込むというところがエンジニアリングなんですけど、それだけじゃなくて実際の音場のアーティスティックな部分もしっかり感じて掴めればいいなと。
自分も音楽を愛して……まあ、「for and by Music Lovers」じゃないですけど(笑)。
やっぱり楽しみながら、愛しながら出来ると良いな、と思いますね。
『宿敵』と書いて『とも』と読む? 開発を振り返って
ニューヨークのエンジニアさんによる、完成したMDR-Z1Rの評価はいかがでしたか?
やはり「エクセレント」?
「エクセレント」でした(笑)。
もちろんその評価に行き着くまでには、結構厳しいことも言われています。
「ここを1dB上げて」とかを、現場でどうすればいいのかと試行錯誤して。
部品が揃ってきている時に、どうしてもその場で直したいところが上がってくるんです。
そこで、日本は日本で色々な素材を検討していたりして忙しいのに、『ここを変えてくれ』って言ったりして。
結構、ケンカしながらやっていたところもあるんですよ。
今なので綺麗ごとのような言い方をすれば、こういう音のこだわりの強い製品なので、最大限リクエストは受けようと、そこは信じて、言われるとおりに変えてやろうと思っていました。
それはもう、潮見さんVS尾崎さんみたいな感じでしょうか。
お互いに譲れないところがあるんですよね(笑)。
電話もしますし、帰ってきたら帰ってきたで、今度は……。
「ちょっといい?」って(笑)。
そう、夜7時から3時間、始まるんですよ(笑)。
お互いにやっぱり、こだわりが強いんですよね。
もちろん、色々とぶつかるところもあるんですけど。
デザインとも同じような関係でやってきて。
やはり、お互いがベストなものを作ろうとしてやってるんです。
今となってこうやって完成した後だと、「ああいうこともあったね」なんていう美談になるんですけどね(笑)。
その場は必死でしたね。
もう、険悪なムードになったり……?
いや、そこは一周回って仲が良い、みたいな感じでした。
良いライバルみたいな(笑)。
『宿敵』と書いて『とも』と読むような感じです(笑)。
潮見さん&尾崎さん的に、MDR-Z1Rは何点なんでしょうか。
もちろん、100点のつもりで作りました。
ただ、時代が進むに連れて、技術も変化して行きます。
例えば今回ですと、新しいマグネシウムドームが使えるようになりました、とか。
そうすると、プロダクトとしての表現の幅も広がります。
音楽の表現自体もデジタルミュージックの登場によって進化しているのと同じように。
作った時は100点だと思いますけど、5年後になると「もっとこう出来ていた、今ならこう出来るかも」って思ってしまうかもしれません。
ベクトルが変わってしまいますよね。
100点の物が5年後に80点になってしまう、とかではなく、評価軸が別になってしまうので。
そうですね。
だからこそ、ここで満足をしていないで、もっと良い物を作ってやろう、という気持ちはありますね。
僕は、例えばMDR-Z7が5万5千円で、僕の中では95点くらいかなあと思っていて。
それがMDR-Z1Rで20万になると、98点くらいになる。
そしたら、あといくら使わせてもらえれば100点の物が出来るのかな、と(一同笑)。
きっと、99.999点とかになるんでしょう(笑)。
どこまでいっても、多分100点っていうのは出来ないんでしょうね。
我々がオンリーワンのものを手作業で作れば、100点の物が出来るかもしれません。
ただ、それを量産するというのは難しい。
我々SONYというのはやはり大きな会社で、色んなプロダクトをやっておりますので、安定して量産するということの技術や、その難しさも知っています。
ただ、やはりこれだけの物を作ろうとすると、量産化の技術が全く立ち行かないような世界があります。
ここから先は職人の技術というか、技能ですよね。技能にかけてみよう、と。
そういったところで思い切れるかどうかが、こういうプロダクトが最終的に完成するかどうかの分岐点になっていたりする。
後から考えてみると、そう感じることがあります。
なるほど。
最後に、こちらから質問を返すのも何なのですが……。
20万円って、高いですか? 安いですか?
ん! えーと、そう、ですね。
……流石に、『安い!』とは、なかなか言えないかな(一同笑)。
ただ、そういう価値観は必ずしも一定のものではないので。
このヘッドホンを聴いて、価格も踏まえて「アリ」と感じるのであれば、それは適切な価格となるでしょうから。
そしてそう感じる方々は、サウンドやスペックから鑑みるに、決して少なくないんじゃないかと思います。
ありがとうございます。
あとは、今回のインタビューのような情報を知れるかどうかでも、かなり認識が変わってくると思います。
商品単体をパッと見ただけではわからない価値というか、こうやってお話を伺って気付いたことって、沢山ありますので。
今日は素敵な機会をありがとうございました!
以上、SONY『MDR-Z1R』の開発者インタビューでした。
あらゆる技術の粋を極めて作られた、SONYサウンドの系譜を受け継いだ新たなるフラッグシップ・モデル。
その魅力、真価の一端に触れられたかと思います。
こちらはe☆イヤホン全店で試聴機をご用意しておりますので、
ぜひ、SONYが送る渾身のサウンドを体感してみて下さいね。
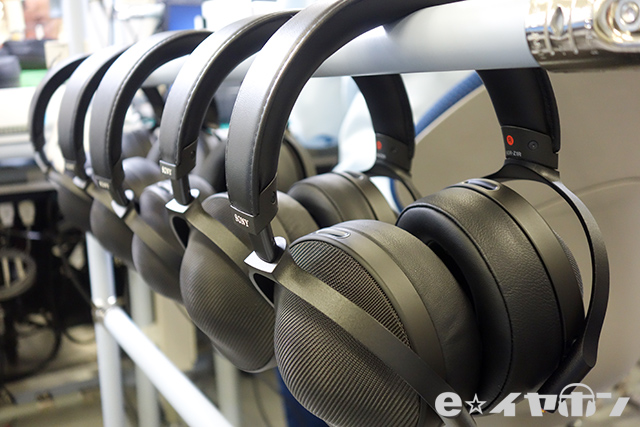
写真はソニー・太陽視察時のもの
お相手はだいせんせいことクドウでした。それではまた次回。
提供:ソニーマーケティング株式会社
※記事中の商品価格・情報は掲載当時の物です。
店舗案内
秋葉原店 本館

ゲーミング AKIBA

大阪日本橋本店

名古屋大須店

仙台駅前店
